500% drop in the carbon footprint of rubber products
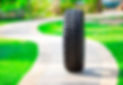
Life Cycle Analysis of Actifine®
Actifine® is largely a circular source of natural rubber and carbon black for tyre and technical rubber compounds. It also replaces a host of other fossil-based rubber compounding ingredients used in tyre manufacturing. Actifine® production combines various micronisation steps and a patented chemical activation process to convert the fine rubber powder into a surface-reactive, high-performance additive.
​
In the current situation, tyre waste is largely incinerated, irrespective of whether it is, for example, temporarily repurposed into artificial sports fields or children's playgrounds. When reusing the rubber as a raw material to produce new tyres (the Actifine® case), the rubber is no longer incinerated, resulting in a circular process that can be repeated over and over.
​
For the life cycle analysis (LCA) calculations, the following scenarios were compared:
-
Natural rubber from old or new plantations: Tyres are produced from, along with other raw materials, natural rubber from either old or new plantations. Tyres will be incinerated at the end of their lifespan.
-
Actifine® scenario: Tyre rubber becomes circular by adopting chemically activated rubber powder pulverised from end-of-life tyres as a new raw material in the tyre manufacturing process.
The COâ‚‚ emission factors of energy sources are based on the Dutch reference data. There is also a significant difference that must be taken into account between COâ‚‚ emissions from rubber plantations older than 60 years and new plantations which usually require burning or cutting down tropical forests.
​
The anticipated overall COâ‚‚ emissions from the annual production of 10 kilo-tonnes of Actifine® product is 26 kilo-tonne of COâ‚‚. In comparison, manufacturing an equivalent quantity of new tyres annually accounts for 103 to 135 kilo-tonne of COâ‚‚, depending on the origin of the natural rubber. This results in a total COâ‚‚-emission savings of 110 kilo-tonne of COâ‚‚ per year, which is 7.8 tonnes of COâ‚‚ per tonne of product.
The production of a tyre using Actifine® requires 4 to 6 times less COâ‚‚ compared to using virgin materials.
​
The results of the analysis are visualised below.

Deforestation by Rubber Plantations
The clearing of rainforests to make place for new rubber plantations is a recent trend with devastating effects on the environment. Substituting Actifine® will reduce the need for increasing future natural rubber capacity, by reusing it. The carbon footprint of rubber products currently produced with natural rubber from new rubber plantations would significantly decrease.
Actifine® Redefines Sustainability in the Rubber Industry
Virgin rubbers can have up to 500% larger carbon footprint than Actifine® which is up for reducing the environmental impact of the industry without compromising product quality.
​
Eco-friendliness of natural rubber unfortunately is context-specific and depends on its source. As long as it is ethically resourced from long-cultivated fields older than 60 years, it has the lowest energy consumption and greenhouse gas emissions among many rubber materials.
​
However, with more demand, recent years have witnessed a surge in tropical deforestation linked to newly developed natural rubber plantations, skyrocketing carbon emissions, triggering habitat loss, biodiversity depletion, pollution, and social issues in the regions where it is produced. Moreover, natural rubber is vulnerable to climate change and disease, which threaten its supply and quality.
​
Synthetic rubbers, on the other hand, are derived from fossil fuels, have a high carbon footprint, and are non-renewable. Despite their characteristics, synthetic rubbers also may have inferior properties than natural rubber for certain applications.
​
That's why Actifine® offers a unique solution for your rubber needs. Actifine® is a functionalised micronised rubber powder that is recycled from end-of-life tyres. Born from a circular stream of a feedstock which would normally be sent to disposal or burning, it combines and ‘embalms’ the best properties of natural and synthetic rubbers solidified in the form of the original tyre compounds.
​
Actifine® emits only 2.6 tonne-COâ‚‚e per tonne-polymer, a carbon footprint that is nominally 50 % of all major synthetic rubbers and elastomers. Although natural rubber from old plantations has an emission factor of 0.7 tonne-COâ‚‚e per tonne-polymer, the plantations younger than 20 years built by deforestation emit as much as 13 tonne-COâ‚‚e per tonne-polymer.
​
By using Actifine®, you can reduce your greenhouse gas emissions, lessen your dependence on virgin rubber materials, save energy and costs, and enhance the performance and durability of your products. As a champion of eco-conscious production and circular economy, it also mitigates deforestation, and minimises the colossal problem of tyre disposal.
​
If you are looking for a way to improve the performance and sustainability of your rubber products, then Actifine® is the solution for you.

Should Waste be Fuel?
A high proportion of tyre waste is incinerated in kilns to help fuel the cement production process. In the absence of high-volume 'circular options', this has been the preferred (even mandatory) destination for tyres for decades. Clearly, a shift towards upcycling and reusing end-of-life tyres in line with circular economy principles is our only way forward.
